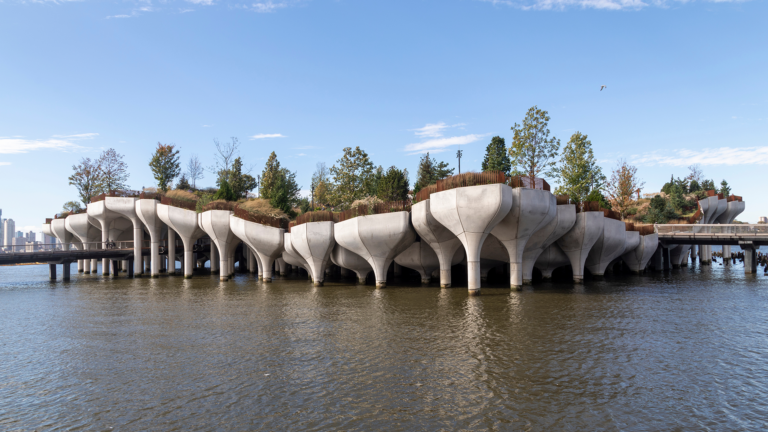
Energy & Environment
Committed to Sustainability
The American Cement Association and its members support market‐based policies and initiatives that will enable the industry’s continued reduction of its carbon footprint.
As an industry, we are proud to work toward our goal of achieving carbon-neutrality by 2050 or sooner while preserving American manufacturers’ global competitiveness. To reach our goal, we need policymakers and agency leadership to work collaboratively with our industry.
Essential Material
Concrete is the world’s most utilized material after water. The U.S. uses about 400 million cubic yards of concrete each year to build highways, bridges, runways, water & sewage infrastructure, schools, high-rise buildings, dams, homes, floors, sidewalks, driveways, and more.
Understanding the cement production process is essential for appreciating this material’s role in the economy and the extensive environmental regulations that the industry complies with.
Manufacturing Cement
-
Cement manufacturing depends on carefully balanced chemistry and physics. Cement plants run continuously—typically 24 hours a day, seven days a week. They use temperatures as high as 2,700 degrees Fahrenheit to convert limestone and other minerals to the active ingredient in cement — clinker. Generating and maintaining kilns at the high temperatures required involves the combustion of significant quantities of fuel. The chemical process to create clinker is also emissions-intensive, typically generating 50 to 60 percent of the CO2 from cement manufacturing.
-
Cement plants are extensive systems with high capital investments, often costing several hundred million dollars to build. Environmental controls and permitting add to the complexity, making any changes to the manufacturing process challenging and costly.
-
Cement and concrete offer significant environmental benefits over the project’s life cycle. Infrastructure constructed with concrete are more energy-efficient, and concrete’s durability reduces the need for frequent repairs and replacements. Concrete also serves as a carbon sink, and through a natural process called carbonation, concrete permanently sequesters CO2.
Solution: A Unified Federal Approach
How This Works
To ensure competitiveness, consistency, and predictability while preserving the goal of net-zero emissions by 2050 or sooner, we encourage Congress to institute market-based policies that protect manufacturers from being subject to both federal and state-based carbon emissions programs.
Download ACA’s Energy-Intensive, Trade Exposed Manufacturing 1-pager
-
A unified federal system would simplify compliance, reduce the burden on manufacturers, allow them to focus on innovation and efficiency, and enhance their global competitiveness. This approach provides the flexibility to select the best technologies and efficiency upgrades tailored to their operations, fostering economic growth and job creation.
-
Consistency and predictability for manufacturers helps them achieve environmental goals more effectively.
Solution: Accelerate Carbon Mitigation Technology
U.S. cement manufacturers have invested billions of dollars in technologies to increase energy efficiency and reduce carbon emissions. Still, energy efficiency alone is not enough to meet long-term carbon reduction goals. More than 60% of the cement industry’s carbon emissions result from the chemical conversion of limestone and other ingredients into cement—there is no way to prevent the generation of CO2 during this process. It is a “chemical fact of life.”
Any long-term carbon reduction strategy to meet the carbon neutrality goals of the cement manufacturing industry require significant advances in carbon capture, utilization, and storage technologies.
Solution: Move to Alternative Fuels
How This Works
The cement industry has a long history of safe and efficient use of alternative fuels, ranging from used tires and biomass to a wide variety of secondary and waste materials, but barriers to using alternative fuels constrain the industry.
-
Cement kilns operate at high temperatures and long residence times, making them efficient at combusting various alternative fuels with low emissions levels. The robust nature of cement kilns allows for the safe and effective use of diverse fuel types, which helps reduce reliance on traditional fossil fuels and supports waste management by diverting materials that would otherwise end up in landfills.
-
Regulations under the Resource Conservation and Recovery Act and the Clean Air Act restrict using non-hazardous secondary materials as fuels. Reducing these barriers can increase the industry’s use of alternative fuels.
-
Reuse is a proven solution. The cement industry can reuse millions of tons of alternative fuels including plastics, biomass, and other landfilled materials as fuel. This reduces materials in landfills and lowers greenhouse gas emissions, supporting sustainability goals.
Solution: Permit Modernization
Regulatory barriers prevent cement manufacturers from investing in technology and process improvements to reduce GHG emissions. Modernizing the permitting process can enable more efficient and environmentally friendly operations.
Downloadable One-Pagers
Get In Touch
Director, Tax, Environment & Energy
Senior Director/Counsel, Government Affairs
Director, Government Affairs