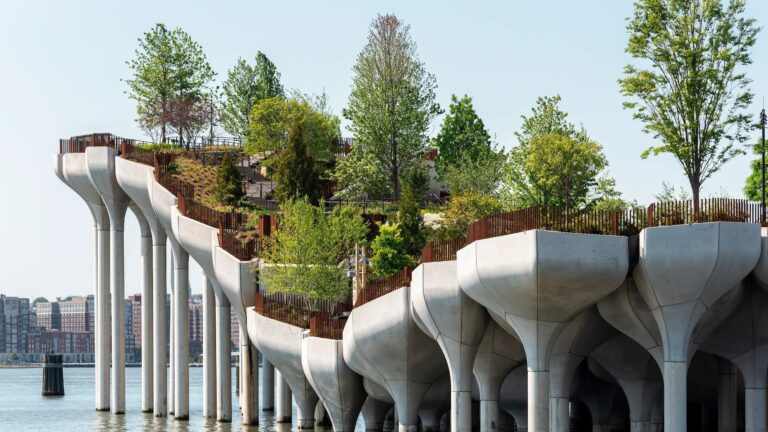
Cement & Concrete FAQ
Cement and Concrete 101
Your basic questions answered.
-
Cement is a key ingredient of concrete, typically making up 10 to 15 percent of the concrete mix by volume. Portland cement and portland-limestone cement are the most common types of cement used in concrete.
In concrete, a paste made of cement and water is mixed with aggregates (sand, gravel, or crushed stone). As the cement reacts chemically with the water, it binds the aggregates into a rock-like mass. Concrete continues to harden and gain strength over time, although most of the strength is developed in the first few weeks after placement.
-
Portland cement clinker is made by first heating limestone, shale, iron ore, and clay in a kiln to 2,700 to 3,000 degrees Fahrenheit. The resulting compound, known as clinker, is then finely ground along with gypsum, limestone, and other materials into portland cement.
Lime and silica make up 85% of the ingredients of portland cement, with alumina and iron oxide as additional components.
-
Portland Cements
Both portland and blended cements are hydraulic cements, that is, they react chemically with water and can do so while under water. There are several types of hydraulic cement, each of which lends itself to particular uses.
Types of portland cement are:
- Type I, for general use applications
- Type II, for use when concrete will be exposed to moderate sulfate conditions
- Type III, for use in applications requiring high early strength
- Type V, for use when concrete will be exposed to more severe sulfate conditions
Portland cements conform to specification ASTM C150.
Blended Cements
Blended cements are mixtures of portland cement and other materials like limestone, blast-furnace slag, or pozzolans (for example, fly ash, silica fume, or natural pozzolans). Blended cements have a lower carbon footprint than portland cements and therefore will reduce concrete’s carbon footprint and can enhance durability.
Types of blended cement include:
- Type IL: Portland-limestone cement (PLC)
- Type IP: Portland-pozzolan cement
- Type IS: Portland blast-furnace slag cement
- Type IT: Ternary blended cement
Blended cements conform to specification ASTMC595. All of these base cement types are suitable for general concrete applications, and special properties like moderate or high sulfate resistance can be verified through testing. When special properties are applicable, additional descriptors are appended the type designation. For example, Type IL(MS) indicates a moderately sulfate resistant portland-limestone cement.
-
Yes, the performance specification for cement is ASTM C1157. This specification has very limited chemical requirements, but has similar requirements to ASTM C150 and C595 for performance characterstics like strength, setting time, and others. C1157 cements are:
- Type GU, General Use
- Type HE, High Early-Strength
- Type MS, Moderate Sulfate Resistance
- Type HS, High Sulfate Resistance
- Type MH, Moderate Heat of Hydration
- Type LH, Low Heat of Hydration
-
PLC is a sustainable and durable cement containing 5% to 15% limestone. It has similar performance to Type I portland cement but with about 10% lower greenhouse gas emissions.
PLC is accepted by all 50 state DOTs, ACI codes, and specifications from the ICC, FAA, and AIA.
-
Standard practice is to measure concrete’s compressive strength at 28 days. This provides a consistent point to measure strength to assure structural performance.
The use of supplementary cementitious materials (SCMs), which significantly reduced the carbon footprint of concrete, can lead to strength development that is lower at 28 days. Therefore, some specifiers have begun specifying 56-day or even 90-day strengths, in order to allow the slower reacting SCMs to contribute to the strength, and durability, of concrete.
-
3,000-pound concrete is concrete with a compressive strength of 3,000 pounds per square inch (PSI) at the 28-day mark. Other strengths may also be specified. High-strength concrete typically has a strength of 8,000 psi (55 MPa) or greater.
-
There is no universal international specification for portland cement. Specifications vary globally, and every country has specific standards, so cements must be tested to ensure they meet national requirements. U.S. and some international specifiers use ASTM C150 for portland cement and ASTM C595 for blended cements. Some state DOTs reference AASHTO M 85 for portland cements and AASHTO M 240 for blended cements. For many years, the technical requirements for ASTM and AASHTO cement specifications have been identical.
Working with Cement and Concrete
Answers to hands-on questions.
-
You can adjust concrete’s strength when designing the concrete before placement. Several variables impact a concrete mixture’s strength, but an important one is the water-to-cement ratio. Everything else being equal, a lower water content results in stronger concrete. Other variables can also impact a concrete mixture’s strength . Quality materials, a good mix design, and proper curing are all key factors. Our publication Design and Control of Concrete Mixtures covers this topic in detail for industry professionals.
-
Concrete made with hydraulic cements, like portland and blended cements, does harden underwater. Portland cement and blended cements are hydraulic—which means they set and harden through a chemical reaction with water. Fresh concrete can even be placed under water and will harden and gain strength.
-
Alkali-silica reactivity (ASR) is the result of alkalies in concrete (most commonly from the cementitious materials) chemically interacting with reactive silica in certain susceptible aggregates. This reaction forms a gel, which can swell and expand in the presence of moisture, and possibly crack the concrete. Common solutions are to use aggregates that are not susceptible to ASR, use of some blended cements, use of many supplementary cementitious materials (SCMs) in sufficient amounts, and reducing the alkali loading of concrete. Detailed guidance for these solutions are found in ASTM C1778.
-
Decorative finishes compatible with concrete surfaces include:
- Color applied as a stain or added to the fresh concrete mixture
- Touchable textures like a smooth polish or rough gravel
- Geometric patterns that you score, stamp, roll, or inlay on the surface
- Slip-resistant coatings
For more information see PCA’s Finishing Concrete with Color and Texture, PA124.
Caring for Cement and Concrete
Answers to your maintenance questions.
-
Using quality materials, a low water-to-cement ratio, and suitable aggregates will all decrease concrete permeability and minimize the impact of aggressive materials. Sealers and coatings can also repel corrosive substances. Sulfate-resistant cement such as portland cement Type II or Type V, or blended cements with (MS) or (HS) designations (for example, Type IL(MS)) are the best choices for concrete that will be exposed to sulfates in soil or groundwater. More detailed information is available in PCA publication, Effects of Substances on Concrete and Guide to Protective Treatments (IS001)
-
Remove stains from concrete using wet or dry methods—choose your approach according to stain type. A degreaser may work on an oil stain, and an acid-based cleaner may lift rust. Dry methods such as sandblasting or grinding may be necessary if a substance has soaked in.
Quick Links
Find more information.