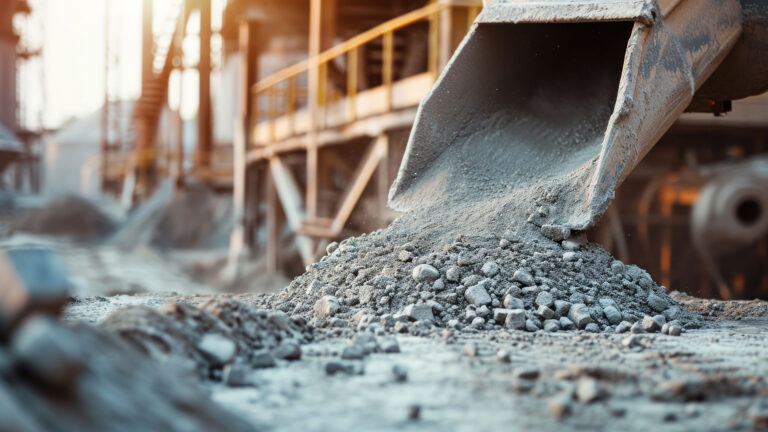
Blended Cements and Sustainability of Concrete Construction
The Future of Cement
Portland cement manufacturers are making progress in reducing the embodied carbon associated with construction by offering a wider range of products with lower carbon footprints. For cement producers, one path to reduce carbon is to decrease their production of portland cement and increase their production of blended cements.
Cement is made by grinding portland cement clinker—the main energy- and CO2-intensive ingredient—along with other ingredients, to a fine powder. Because of efficiencies of scale, and engineering development over more than 100 years, modern clinker production is among the most efficient industrial processes. Blended cements have lower carbon footprints than portland cement because they allow for increased quantities of non-clinker ingredients. Replacing some of the clinker in portland cement reduces the embodied CO2 of cement, and cement-based materials made from it, including mortars, grouts, and concretes.
What is PLC?
PLC is one of four blended cement types described in ASTM C595, Standard Specification for Blended Hydraulic Cements, and its AASHTO counterpart, M 240. For portland-limestone cements (PLC, or Type IL), ground limestone is included as a cement ingredient at quantities from 5% to 15%, which is up to 10% higher limestone content than portland cement. PLC reduces carbon footprint by up to 10% when replacing portland cement in concrete mixtures. In mid-2023, total shipments of portland-limestone cement (PLC) across the U.S. exceeded those of portland cement (ASTM C150, AASHTO M 85), making PLC the dominant cement type for general concrete construction.
Blended Cements
Other blended cements are made using pozzolans and slag cement. These materials can come from other industries, such as coal ash (fly ash or other coal combustion residuals) from electricity production; slag cement from steel manufacture; or can be mined and processed specifically for use in cement production, such as calcined clays or shales. There are also ternary blended cements (Type IT) that include multiple types of these ingredients. These other blended cement types – Types IP, IS, and IT – can have even smaller carbon footprints than PLC primarily for two reasons: higher proportions of non-clinker materials are allowed, and those materials, like limestone, have very low carbon footprints. The availability of these other materials varies by location, so part of the work of cement manufacturers is to explore what other ingredients are available to them and what cement formulations they can produce with those materials.
The Impact of PLCs
A holistic approach to sustainability encompasses many aspects designed to improve construction practices, including: more efficient use of natural resources; use phase impacts such as better thermal performance of buildings and fuel economy of vehicles on pavements; and optimized concrete mixture proportions and structural design, and efficient construction practices. Environmental leaders, whether in industry or government, have placed an early emphasis on reducing embodied CO2 emissions, with a longer-term goal of including other life cycle impacts. A key metric of the footprint of materials is described in terms of greenhouse gas (GHG) equivalents or global warming potential (GWP). A Product Category Rule (PCR) is used to assess environmental impacts, which can be reported via different documents, the most common of which are Environmental Product Declarations, or EPDs. In 2021, PCA published an industry average EPD for four different categories of cement: portland cement, blended cement, portland-limestone cement, and masonry cement.
Modifying a concrete mixture design to replace higher carbon materials with lower carbon ingredients is one of several strategies to reduce the environmental footprint of concrete construction. In concrete, the reduction of clinker content represents the biggest opportunity for GWP reduction of the materials. Whether the reduced clinker content of the concrete is obtained by using blended cements, SCMs added to concrete, or a combination of these practices, when a concrete mixture design changes, testing is needed to determine the effects on fresh and hardened concrete properties. Like portland cements, PLCs are compatible with all supplementary cementitious materials (SCMs), and substituting PLC for portland cement allows for similar usage of SCMs. For other types of blended cements, using SCMs in the concrete mixture requires additional consideration by the concrete producer.
Building a Brighter Future
Other than water, concrete is the most-used material on the planet, representing on the order of half of all manmade materials by mass. Because society places so much concrete each year, even small changes to its formulation can have dramatic effects on the construction industry’s annual carbon footprint—to the benefit of everyone. For instance, the use of PLC and other blended cements in the U.S. in 2023 reduced CO2 emissions by 3.9+ million metric tons, which the U.S. EPA says is the equivalent of the carbon stored in 4.5 million acres of U.S. forests for an entire year.
As a key part of the construction industry, cement manufacturers are working to reduce their impact on global climate change. They recognize that they can play a big role and continue to innovate for cement formulations with even more favorable environmental performance. PLC has shown the industry that it is possible to evolve their manufacturing processes to offer the design and construction communities new cements to produce resilient and sustainable concrete.